In June 2022, InterGroup was appointed by Channel Infrastructure (formerly Refining NZ) to provide manual industrial tank cleaning services. This formed part of the decommissioning stage of the transition from a refinery to a terminal storage facility, with some tanks earmarked for a change in product service. We have cleaned approximately 40 tanks, previously used to store crude, finished fuel and other hazardous substances. With tanks allocated different priority levels aligned to the terminal transition sequence and schedule requirements, the project was split into two groups and is now nearing completion.
Marsden Point Manual Tank Clean with Channel Infrastructure
The Project
Led by our Area Manager Ryan Naidu, and drawing on the expertise and experience of the Northern Industrial Operations and Administration teams – as well as our National Compliance Management team, we planned, programmed and delivered safe and efficient work – meeting all the client’s time, cost and broader delivery requirements.
Zone 0 Non-Man Entry Robot
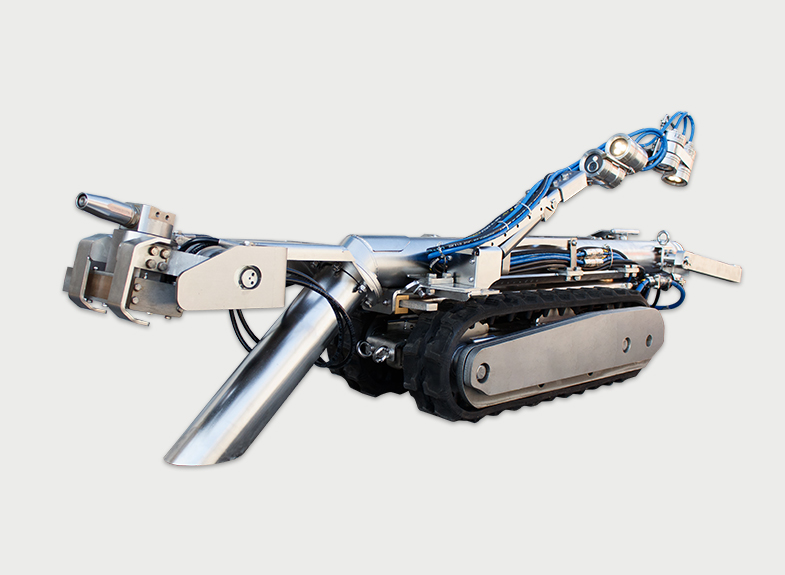
Delivering Strong HSE Performance
With a ‘No Spill’ culture and high safety and environmental standards, a strong performance in this regard was vital to the client and is always front of mind for Intergroup. Our existing presence at the refinery meant we brought a depth of familiarity with the client’s systems and procedures. This helped us to meet the ongoing challenge of successfully delivering multi-disciplined work site packages within this extremely high-risk operational environment. We delivered exceptional environmental and safety outcomes with zero spillages and loss of containment and 45,000 manhours without a safety incident. This was achieved through the implementation of our expertly designed methodologies and by minimising manned entry through the use of the Gerotto robotic system.
What We Did
Our dedicated and expert team has delivered sludge removal and detailed cleaning of 33 hydrocarbon tanks, including nine large diameter floating roof crude tanks via confined space man entry requiring breathing apparatus and extensive health and safety planning. Detailed cleaning has been to a class II/IV level of cleanliness as dictated by the intended re-purposing of the tank. In total, around 4000m3 of sludge has been removed from crude tanks. Tank cleaning works have been delivered through a range of methods – manual, magnetic (utilising our Verti Drive magnetic tank cleaning robot) and, for heavy sludge intensive crude oil tanks, our new Gerotto Zone 0 robotic tank cleaning system.
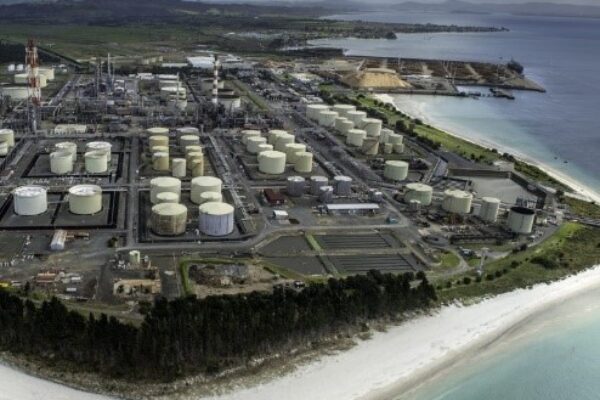
The Marsden Point site is being transitioned to a terminal storage facility, requiring complex industrial tank cleaning under highly challenging conditions
Meeting complex Challenges
Numerous and varying challenges were faced by our team on-site. Frequent changes to the tank availability schedule, based on the terminal transition plan, impacted on the management, planning and delivery of the project works. Regular and clear communication with the client was vital to integrate these, and our agile approach and strong client relationships helped to keep the works running smoothly and within the required timeframes despite required changes.
Integrating and operating the new technology (Gerotto) with no past experience was also challenging for our team on the ground. However, understanding the wide-ranging benefits of using this new system, we invested time in familiarising appropriate staff with the optimal operation of the robot – and the challenge very quickly became an opportunity realised.
Adding Value through Innovation
InterGroup has an impressive history of introducing innovative technology into New Zealand. This project benefited greatly from our approach to challenging the status quo – bringing in the Gerotto Lombrico robotic system which, while widely used to de-sludge and clean crude tanks in refineries in Western Europe, was a first for New Zealand.
Designed and certified to operate in an explosive atmosphere where the risk is continuous, this remotely operated crawler fits through a standard 24” manway and enhances efficiency by being able to be deployed immediately upon removal of the manway cover. This reduces both the required manpower and tank cleaning time. In addition, it provides significant health, safety and environmental benefits by eliminating exposure to toxic waste and the need for a nitrogen blanket or tank venting.
As well as being Zone 0 rated, the unit is fitted with a low pressure and volume jet nozzle system, used to introduce diluted cutter stock to agitate and fluidise the sludge. This feature enables the sludge to be easily vacuumed through the system and the fluidised sludge then extracted from tanks via the head of the “ATC” with sludge vacuumed using High Capacity 3A Vac Trucks
Added Value of our Industrial Team
The value of our technical expertise and ability to problem solve as we go was demonstrated on the T04 (crude tank conversion to Jet-A1). This required a first of its kind solution, to provide a full internal shell clean without any resulting jet contamination.
Despite the complex nature of the work, InterGroup’s experienced industrial team delivered to the required quality standards and within the cost and schedule we had committed to CHI.